
Undercutting is removing some material from the base of the gear tooth to avoid interference. It’s important to note, this is not the same as the outside diameter of the gear. This can be seen in the diagram within the Spur Gear dialog. The pitch diameter, which is read-only, is the diameter of the gear used for spacing the gears.

You can then create a hole with the hole command, which provides more options and makes it easier to alter later on. This will omit the creation of the hole when the gear is generated. It’s important to note, the hole size can be set to zero. The value entered will determine the diameter of the hole. The hole diameter is also straightforward. Simply select the top face of the gear > right-click > select “press pull” > drag or type out the desired dimensions. Thankfully, the height can still be altered after using the Spur Gear generator. The gear thickness represents the extruded height of the gear. Too large of a radius will produce an undercut.Īn undercut will prevent the gear teeth from correctly meshing with each other. You will have to be cautious even when your root fillet radius does not surpass the maximum. You will get a warning message at the bottom of the dialog if your value is higher than allowed. Your root fillet radius must not surpass the maximum value. The root fillet radius is the curvature between the tooth surface and the tooth root. 15mm works well, as that gives a total clearance of. You will want to use a backlash if you’re planning on 3D printing the gears. It also provides space or lubricating oil or grease to be applied between the teeth. The clearance prevents overheating and tooth damage. This is critical to let the gears mesh without binding the gears. The Backlash option lets you define a clearance between teeth of the mating gear. The number of teeth option lets you define how many teeth are placed around the gear. This option will only show up when the Standard is set to English. The diametral pitch is, by definition, the number of teeth divided by the pitch diameter.
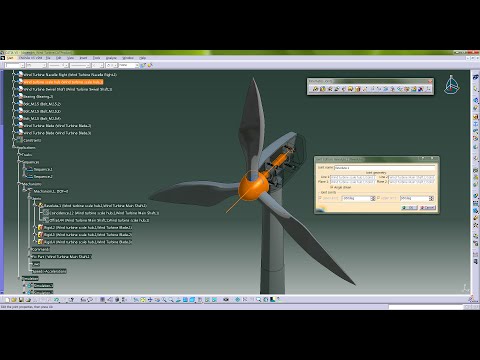
The module is only available when the Standard is set to Metric. The gear module is the unit of size or ratio of the gear’s pitch diameter divided by the number of gear teeth. It is more precisely the angle at a pitch point between the line of pressure (which is normal to the tooth surface) and the plane tangent to the pitch surface. The pressure angle of a gear tooth is the angle between the tooth face and the tangent gear wheel. This is a personal preference, but note that it will also change one of the options (as noted below). The standard option lets you choose from English or Metric units. The following gear details are options that can be altered in Fusion 360 (Spur Gear plugin) The dialog of Fusion 360’s Spur Gear add-in This will help you avoid common mistakes and errors that prevent the gears from working. You should be familiar with the gear terminology before 3D printing any gears. Simply fill out the gear details and the add-in will automatically generate your gear. Both work the same, so it doesn’t matter which one you choose.
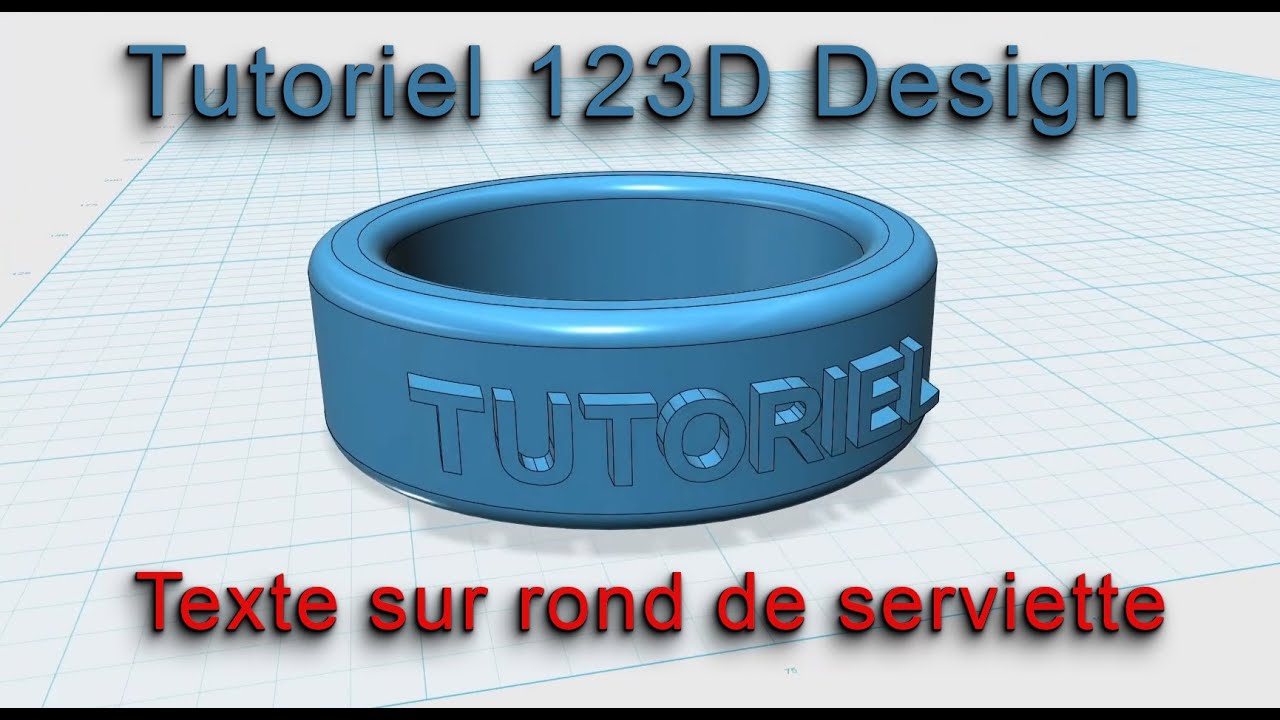
One written in C++ and one written in Python. Select the Tools tab > Scripts & Add-ins > Add-ins Tab > Scroll down until you can see the “Spur Gear” generator. Fortunately, one of the sample add-ins is a Spur Gear generator. Creating gears in Fusion 360 is easier than most think.Įach copy of Fusion 360 includes a few sample add-ins.
